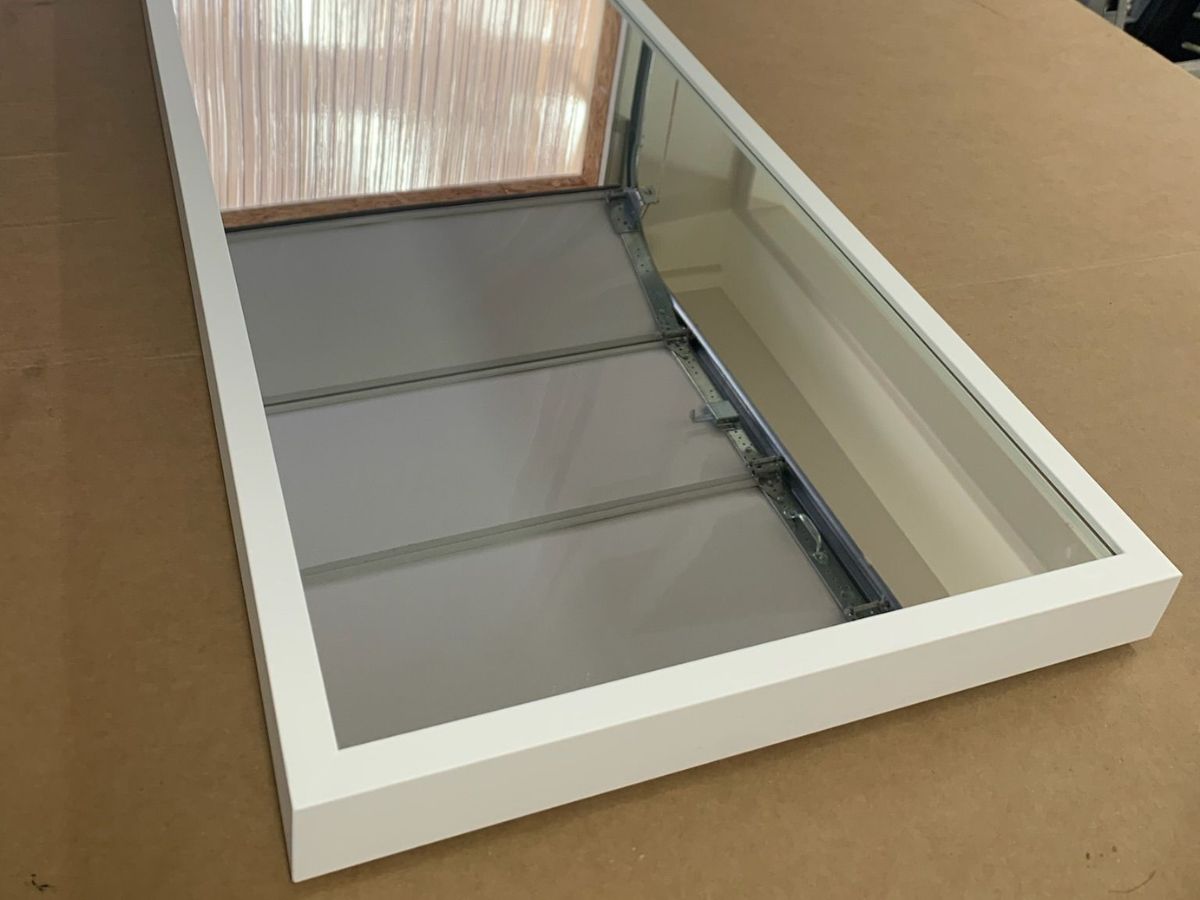
Behind the Scenes: Crafting Custom Mirrors
Custom mirrors are more than mere reflective surfaces; they are integral design elements that enhance aesthetics and functionality in interior spaces. Understanding the meticulous process behind their creation can provide interior designers and remodeling professionals with valuable insights into selecting the perfect mirror for their projects.
1. Selecting the Glass
The journey begins with choosing high-quality float glass, renowned for its clarity and uniform thickness. This type of glass serves as the ideal canvas for mirror production due to its smooth surface and optical purity. The selected glass is thoroughly inspected to ensure it is free from imperfections that could affect the final product’s quality.
2. Cutting and Shaping
Once the glass is selected, it is cut to the desired dimensions using precision tools. For custom mirrors, this step is crucial as it allows for unique shapes and sizes tailored to specific design requirements.
3. Polishing the Edges
After cutting, the edges of the glass are polished to remove any sharpness and to enhance safety and aesthetics. Depending on the design specifications, edges can be finished in various styles, including flat polish, beveled, or rounded edges, each contributing a distinct look to the final mirror.
4. Cleaning and Preparation
Before applying the reflective coating, the glass undergoes a thorough cleaning process to eliminate any contaminants. This typically involves washing with deionized water and specialized cleaning agents, followed by air drying in a controlled environment to prevent dust particles from settling on the surface.
5. Applying the Reflective Coating
The core of mirror manufacturing lies in the application of the reflective layer. Traditionally, a process known as “silvering” is employed, where a thin layer of silver nitrate is chemically deposited onto the glass surface. In modern practices, aluminum is also used for its durability and reflectivity. This metallic coating is then protected with a copper layer to prevent oxidation.
6. Protective Backing
To safeguard the reflective coating, a protective paint layer is applied to the back of the mirror. This not only prevents physical damage but also seals the coating from moisture and other environmental factors that could degrade its quality over time.
7. Customization and Enhancements
For bespoke designs, additional customizations are performed. This may include sandblasting for decorative patterns, adding tints or antique finishes, and incorporating safety features like vinyl backing. These enhancements allow designers to align the mirror with the overall aesthetic of the space.
8. Quality Inspection
The final step involves a comprehensive quality inspection to ensure the mirror meets all specified standards. This includes checking for surface imperfections, verifying dimensional accuracy, and assessing the clarity and uniformity of the reflective coating. Only after passing these rigorous checks is the mirror deemed ready for installation.
The creation of custom mirrors is a blend of art and science, requiring precision and attention to detail at every stage. Understanding this process underscores the value of craftsmanship in delivering mirrors that are not only functional but also elevate the design narrative of any space.